Building Services Modules: Challenge or Catalyst for Serial Renovation?
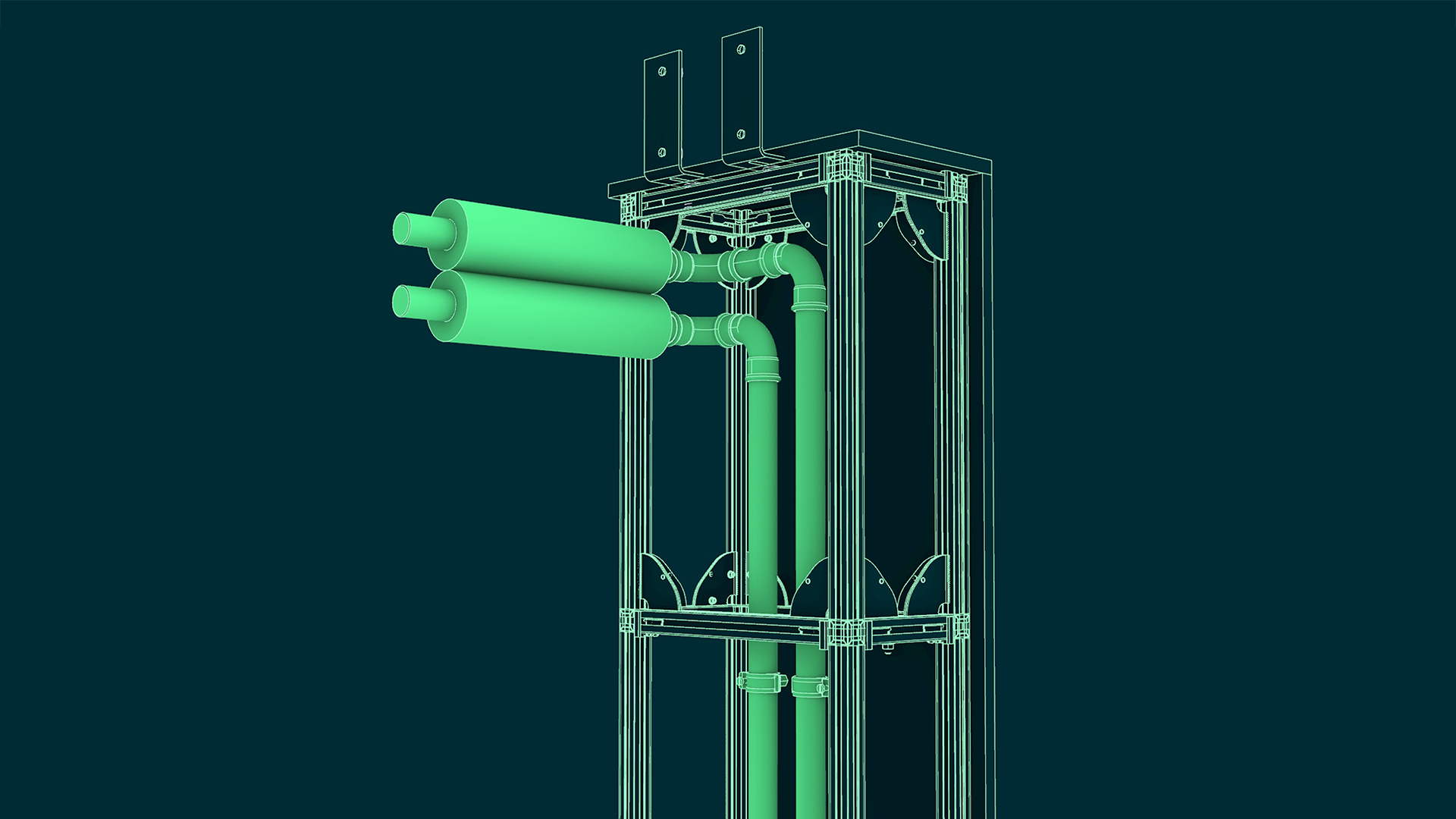
When people think of serial renovation, they usually picture prefabricated facade and roof elements being installed at impressive speed. While the building envelope is quickly upgraded to new-build standards, experts often focus on what’s happening inside: the building services. Upgrading heating, ventilation, and plumbing in occupied buildings is considered one of the biggest challenges for a fast, scalable energy transition. But it’s not an insurmountable barrier. In fact, it is the critical point where a holistic renovation approach, like the one we use at ecoworks, can truly demonstrate its strengths.
The Challenges of Upgrading Building Services in Existing Buildings
The main problem with renovating building services in existing structures is the complexity and individuality that have developed over decades. Old piping networks, a mix of radiator types, and decentralized gas boilers in every apartment pose huge challenges for traditional renovation concepts. Switching to a climate-friendly heating system, such as a centralized heat pump, is much more than just replacing equipment. It requires a completely new system design that works with lower flow temperatures and only operates efficiently in combination with a highly insulated building envelope.
This is where non-integrated approaches fall short. Simply upgrading the facade does not solve the building services problem. In fact, it actually makes addressing it even more urgent.
An Integrated, Serial Approach to Renovation
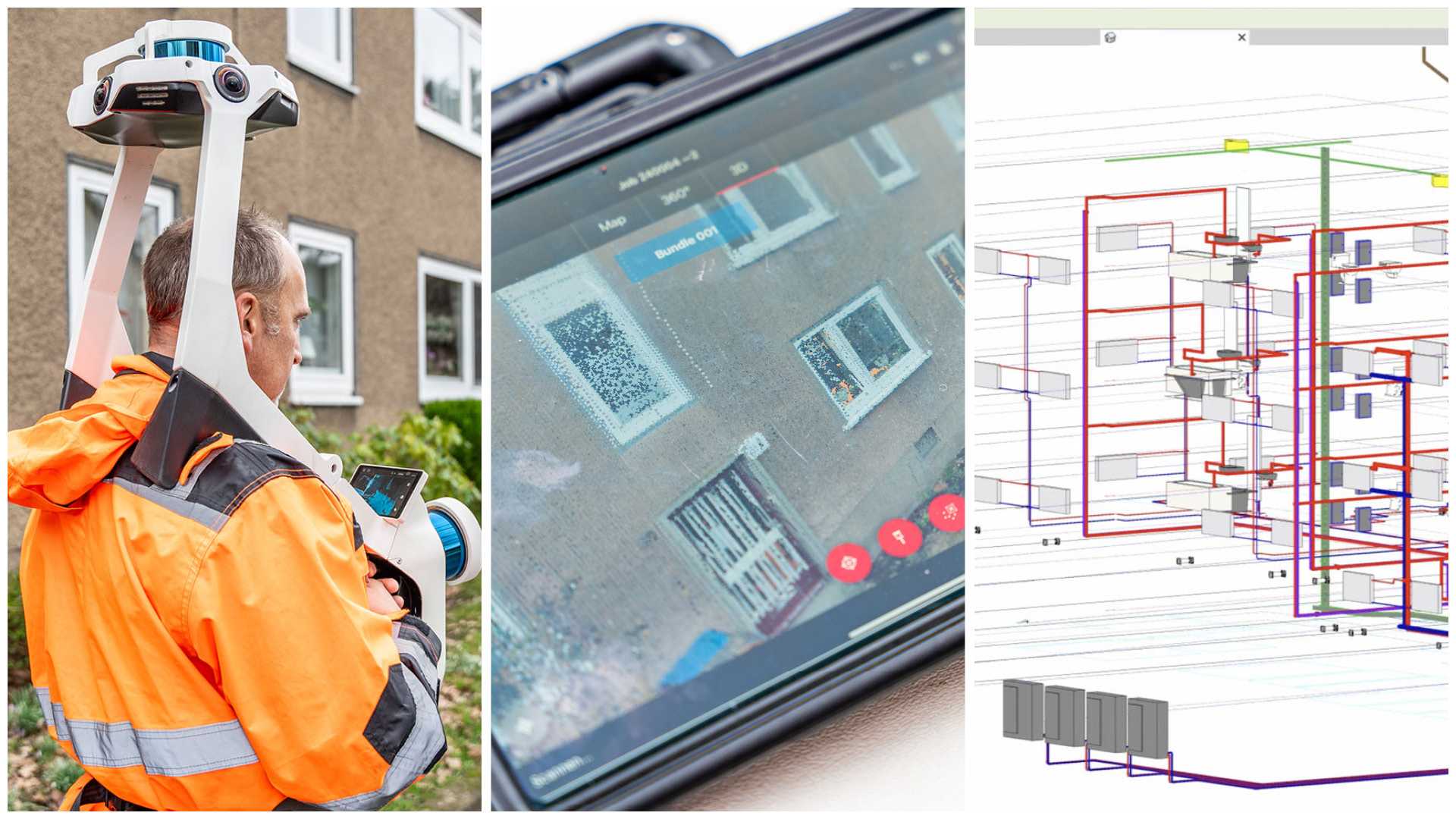
A modern, serial renovation approach considers the building envelope and building services together from the very beginning. The process starts with a complete digital scan of the building using 3D laser technology, capturing not only the exterior but also the existing building services installations. A digital building model (BIM) is then used to plan the new, centralized, and highly efficient energy system.
Instead of assembling all the complex building services on-site, which is made even harder by the shortage of skilled tradespeople, the value creation shifts to a controlled, weather-independent factory environment. Here, prefabricated Building Services Modules are produced as compact units and delivered to the construction site. These already contain the heat pump, buffer storage, and all the control technology, and only need to be connected on-site to the also standardized and prefabricated supply lines. Apartment transfer stations and decentralized ventilation units with heat recovery, which can be easily integrated into the new facade elements, are also part of this system.
Work inside the apartments is kept to a minimum, which significantly increases tenant acceptance and drastically shortens construction time. Building services are not the enemy of serial renovation. Quite the opposite, an industrialized and digital approach makes complex upgrades manageable, scalable, and predictable. What was once a stumbling block is now a catalyst, enabling the energy transition in existing buildings and paving the way to climate-neutral standards like NetZero.
Continuous Improvement: The ecoworks Building Services Module
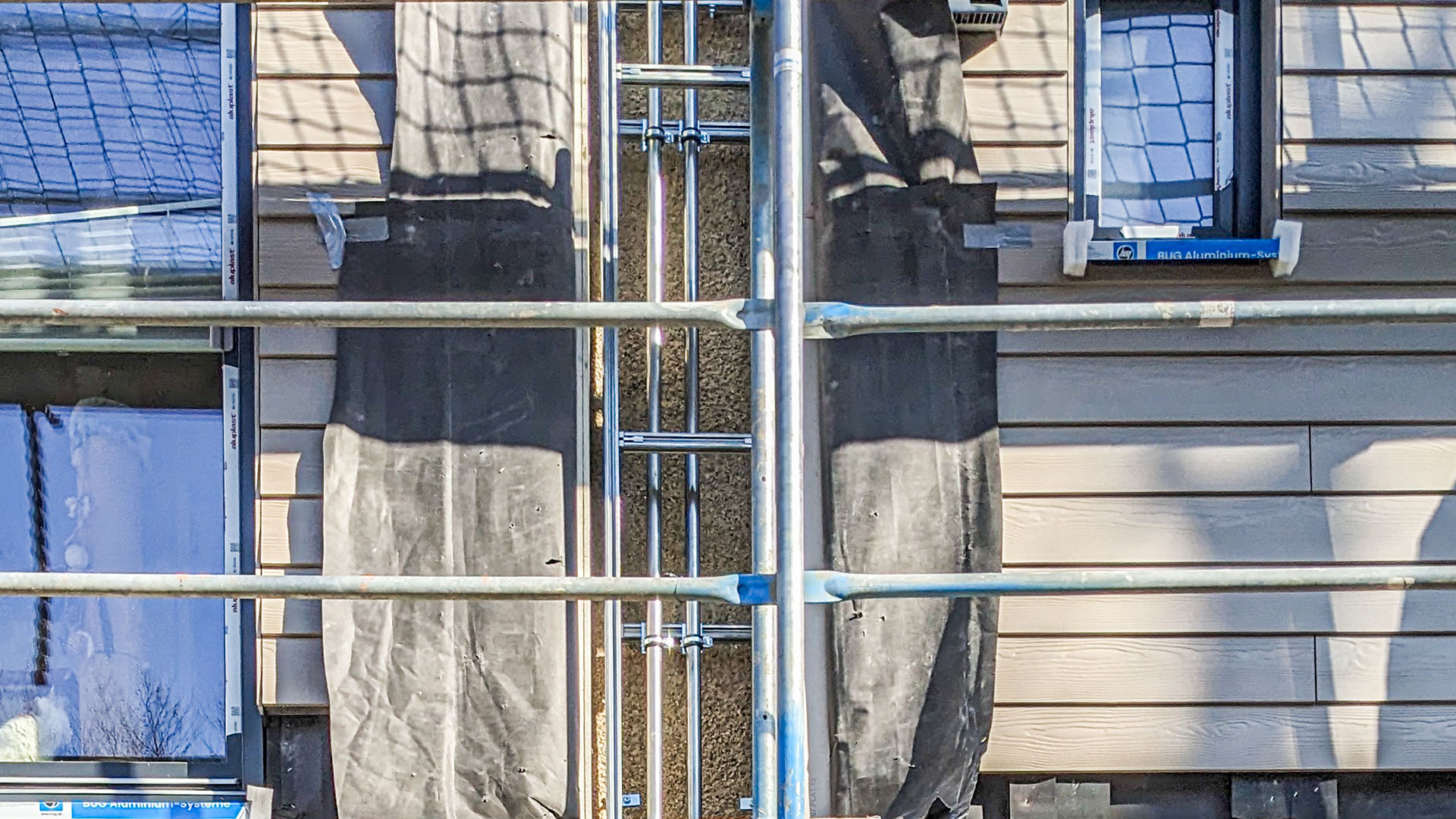
At ecoworks, we are constantly optimizing our processes and planning to make residential buildings climate-ready faster and more cost-effectively. Our facade-integrated Building Services Module is central to this. It is a prefabricated component that combines heating, cooling, ventilation, plumbing, and electrical systems into one compact unit. Renovation is fast, clean, and carried out mostly from the outside, minimizing disruption for residents.
Our modules are industrially prefabricated, removable, and can be installed on-site much faster than traditional systems. Installation is largely independent of other trades or preliminary work. While conventional building services installations often require coordinating several companies, serial prefabrication and assembly require far fewer. This can reduce project timelines by up to 75 percent and significantly lower complexity.
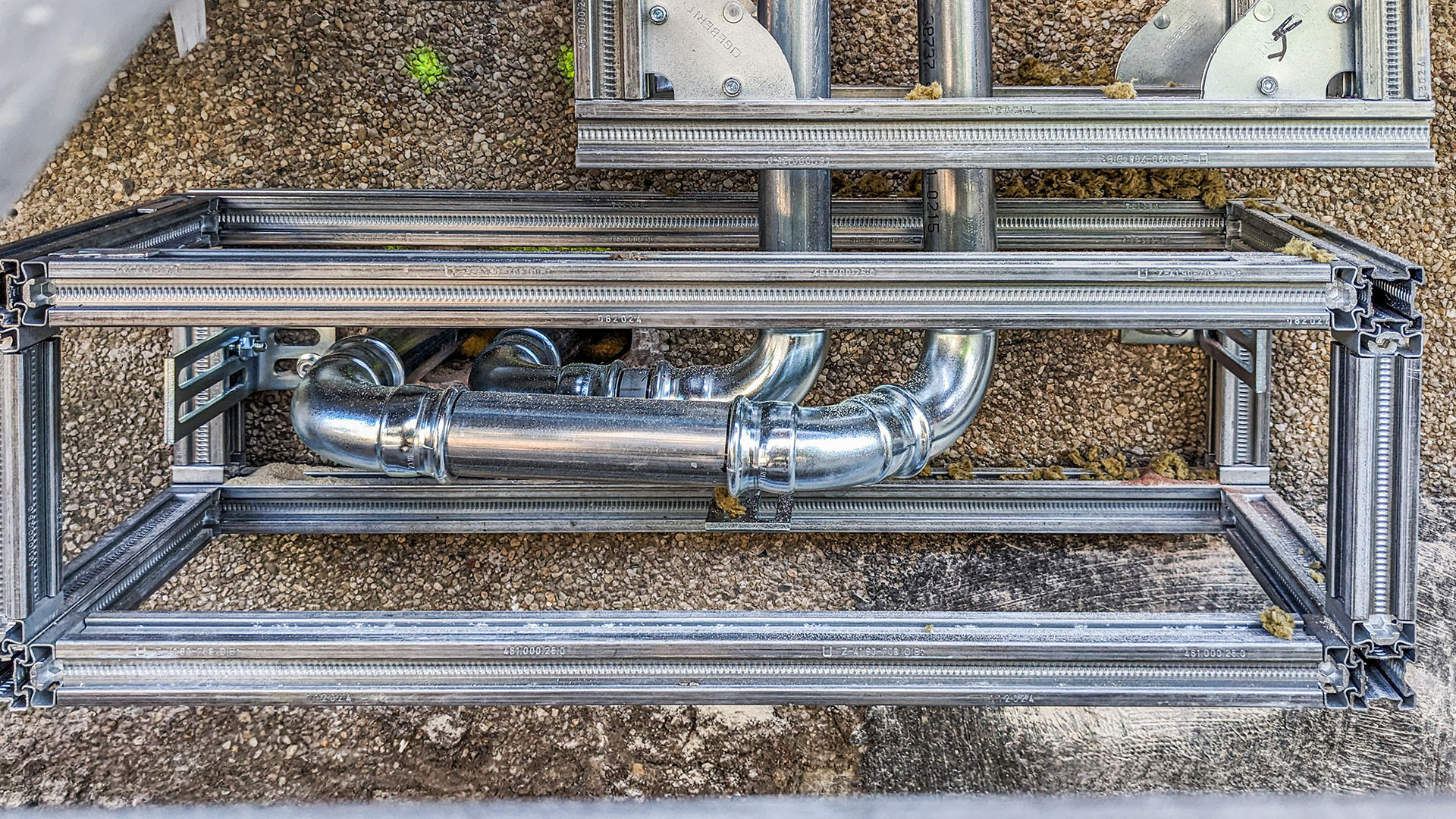
For our clients, this means many advantages: easier inspections, clearer site supervision thanks to standardized components, faster completion, and a cleaner, more efficient construction site. With precise planning and prefabrication, we can also cut overall costs by up to 30 percent.
See how the installation works in our timelapse video featuring highlights from our Hattingen project: